Plasma cutter purchasing advice: how to choose the right product
- What You Need to Know
- Plasma cutters are suitable for fast and precise cutting of conductive metals.
- metals.
- The working temperature of plasma cutters can be up to 30,000 degrees Celsius.
- temperature.
- There are plasma cutters in various designs for private users,
- craft/commerce and industry.
- Simple plasma cutters for do-it-yourselfers are available from around 250 euros.
Plasma cutter – powerful tool for metal cutting
A plasma cutter is a versatile, powerful tool used to cut conductive metals such as steel, copper, aluminium or stainless steel quickly and precisely. It has long been impossible to imagine craft, trade and industry without the power torches. Private users and do-it-yourselfers have also discovered the advantages of plasma cutters. However, there are big differences between low-priced devices for beginners and hobby craftsmen and elaborately designed plasma cutters for industrial use. Here you can find out which types of equipment are suitable for which applications and what you need to look out for when buying a plasma cutter.
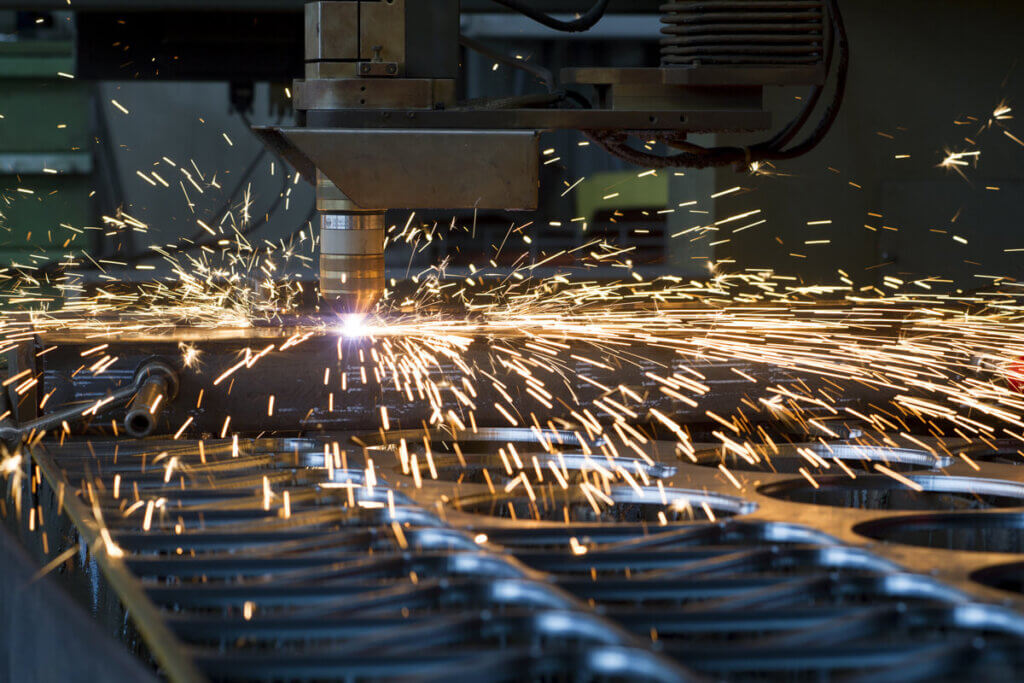
How do plasma cutters work and what are their advantages?
Unlike flex or cutting torches, plasma cutters generate a high-energy plasma of up to 30,000 degrees to cut the material. The working nozzle can be guided freely in all directions by hand or by machine. This makes it possible to work very quickly and to cut very precisely with exact, rounded cutting edges – even on thicker workpieces. And last but not least, a plasma cutter also allows irregular or curved cutting paths that would be difficult to achieve with a Flex, for example. The plasma cutter thus offers practically unlimited possibilities for shaping sheet metal and metal plates up to several centimetres thick. This makes it a versatile tool not only for the metalworking industry, but also for home users, allowing free design.
What is plasma?
Basically, substances can exist in three states of aggregation: solid, liquid or gaseous. The form in which a substance exists depends on the ambient temperature and pressure. For example, water is liquid at normal atmospheric pressure and a temperature between 0 and 100 degrees Celsius. If the temperature falls below 0 degrees (freezing point), it takes on a solid form; if it rises above 100 degrees (boiling point), it becomes gaseous. If you heat a gas further, it begins to accumulate free charge carriers, negatively charged electrons or ions. This highly energised gas mixed with charge carriers is called plasma or “fourth state of matter”.
Plasma cutters use a welding power source to generate a strong arc. This arc is created between the workpiece, which acts as the anode, and the cathode at the tip of the handpiece. It is focused at its exit point on the unit by means of a copper nozzle and generates the plasma, which is between approximately 15,000 to 30,000 degrees hot and vaporises the surface of the workpiece with pinpoint accuracy. The metal vapour is blown away by a compressed gas jet and cools down quickly.
Compressed air is usually used as the gas. Many machines do not have an integrated air compressor and must therefore be operated with an external compressor – a point to consider before purchasing. In order to obtain the best possible cutting edges or to reduce corrosion at the cutting edge, the user can also use special protective gas, provided the equipment is designed for this.
Industrial plasma cutters
- Cutting capacity up to 200 millimetres
- Usually more complex to operate
- Tends to require more accessories
Plasma cutters for home use
- Cutting capacity up to 8 or 12 millimetres
- Simple operation
- Tends to require fewer accessories
Differences between industrial plasma cutters and devices that are also well suited for home use.
The extreme heat of the plasma (for comparison: a welder delivers approx. 3000 degrees) makes it very easy and quick to cut even materials that are several centimetres thick. Plasma cutters, for example, very effectively reduce the production times of metal parts in industry and thus the manufacturing costs. High-energy torches are also very popular on construction sites and in metalworking workshops and craft businesses because of their precision and time savings.
Basically, however, a plasma cutter is suitable for anyone who often needs or wants to cut metal to size accurately and precisely – even in their own hobby workshop. Before buying one, however, you should consider what power is needed. If only thin sheets are to be processed, a simple device with a cutting capacity of up to 8 or 12 millimetres is perfectly adequate.
Are there also plasma cutters for non-conductive materials?
Basically, a distinction can be made between plasma torches with a transferring arc and those with a non-transferring arc. The first type is more common; it is usually referred to when talking about plasma cutters and is suitable for processing current-conducting metals. Plasma cutters with a non-transmitting arc have both the cathode and anode in the handpiece, so no current-conducting material is needed to create the arc. They can also cut other non-conductive materials such as glass or concrete and are intended more for commercial use in industry and on construction sites than for private use.
HF ignition or lift-arc ignition?
Another distinguishing feature of plasma cutters is the way the arc is ignited. High-frequency (HF) ignition is technically more sophisticated. With this method, the arc is created at the touch of a button by using high-frequency current. It is found not only in high-priced units, but also in lower-priced ones. Many devices have the simpler lift-arc ignition instead. Here, the arc is created by briefly placing the handpiece with the current-carrying electrode on the workpiece and then lifting it off. The technique is less convenient, but just as reliable.
What types of plasma cutters are there?
Apart from the basic classification into plasma cutters with transferring and non-transferring arc, plasma cutters can be distinguished above all
- according to their cutting capacity,
- according to the gas or gas mixture used,
- by models with integrated or external compressor,
- according to their own weight,
- according to technical features such as cooling or power requirements, as well as
- according to manual and machine guidance.
Classification according to cutting power
Industrial plasma cutters have a cutting capacity of up to 200 millimetres – they can even cut twenty-centimetre-thick metal effortlessly. For household use and processing sheet metal, simple models with a maximum cutting capacity of 12 or 15 millimetres are usually sufficient. More power is required to cut steel plates 20 millimetres thick and more into shape. The devices are more complex in design and correspondingly more expensive.
Classification according to gas or gas mixture
Many simple plasma cutters are designed for use with compressed air. The use of nitrogen or special gases allows a finer adjustment to the material properties and provides a higher cutting quality. More complex tasks are made possible by dual gas or mixed gas torches, which produce a so-called quality plasma. It allows high-precision cutting of a wide variety of metals in the highest quality. These specialised torches are correspondingly expensive and are mainly found in industry and trade.
Integrated or external compressor
Units with an integrated compressor are usually more convenient to use and do not require external accessories. The built-in compressor corresponds to the performance requirements of the appliance, which makes handling easier. If an external compressor is necessary, it must of course be suitable for the plasma cutter. For this purpose, it is not the suction capacity that is decisive, but the effective delivery volume provided by the compressor, which is also specified in litres per minute (L/min) – do not confuse the two!
Dead weight of the plasma cutter
Is the plasma cutter only used in the workshop at home or does it have to be transported frequently? If the latter is the case, it should not only be lighter, but also have transport protection options.
Cooling and power requirements
For the workshop at home, the most suitable equipment is that which can be operated with normal household electricity. Other units require a high-voltage connection. For plasma cutters with relatively low cutting power and amperage, air cooling is sufficient; for more powerful units with currents above 200 amperes, it should be water cooling.
Hand-guided or machine-guided
Private users usually use hand-guided devices. Machine-guided or computer-guided plasma cutters are mainly found where the highest precision is required, for example in the production of machine parts.
What previous knowledge is necessary to use a plasma cutter?
Basically, no special knowledge is necessary to work with a plasma cutter – the handling is even relatively easy compared to other types of equipment such as welding machines. Nevertheless, the dangers arising from the use of the powerful devices should be taken very seriously. Strong electric currents, flying sparks, steam generation and extremely high temperatures can lead to serious injuries or even death if used improperly. Therefore, the safety instructions in the manual supplied must be followed meticulously.
Complete beginners who have never had anything to do with metal processing should definitely have an experienced person instruct them in its use, show them the assembly and disassembly routines (for example, after-cooling) of the unit and process their first workpieces under supervision. As always, no master has fallen from the sky – so it is best to start with a few trial workpieces. As a rule, it is more experienced people who will use a plasma cutter. But even they should be sure to read the operating instructions and safety instructions when working with a plasma cutter for the first time.
How to find the right plasma cutter for you
Choosing the right plasma cutter depends on several factors. For example, before buying a plasma cutter, you should ask yourself whether you want to use it only once in a while or on a regular basis. Beginners usually have different demands on their device than advanced users. The scope of performance and the accessories of the device are also important purchase criteria. In order to be able to work safely with the plasma cutter, some accessories are indispensable, while others are optional. Therefore, it is important to pay close attention to the accessories, even in the case of bargains, because on closer inspection many of these special offers quickly lose their appeal.
What do you have to look out for when choosing?
Plasma cutters are high-precision devices that generate high temperatures during use. That’s why you should only buy equipment that has a seal of approval, so you know that it meets current safety standards. The plasma cutter should therefore definitely have a GS or TÜV seal. Well-made plasma cutters are available at relatively low prices. In comparison, alleged bargains are often not only less durable, but can also pose a real safety risk.
The cutting power and the current voltage of the plasma cutter should match the subsequent application tasks. For simple cutting jobs, a current voltage of 40 amps is usually sufficient. If you want to cut thicker metals, different metals at once or a wider range of metals, you should definitely check carefully whether the plasma cutter is suitable for these tasks. The cutting performance of the various models ranges from less than 1 millimetre up to 40 millimetres. Also important are ignition power and open-circuit voltage. Correct ignition performance depends on the open-circuit voltage being at least 50 volts when the plasma jet is not activated.
For those who not only have cutting work to do, but also welding work, a combination unit that can do cutting and welding work may be attractive. Another important point that can save a lot of trouble in practice is the cable length. One should make sure that the mains cable and the earth cable are of sufficient length to allow comfortable and trouble-free working.
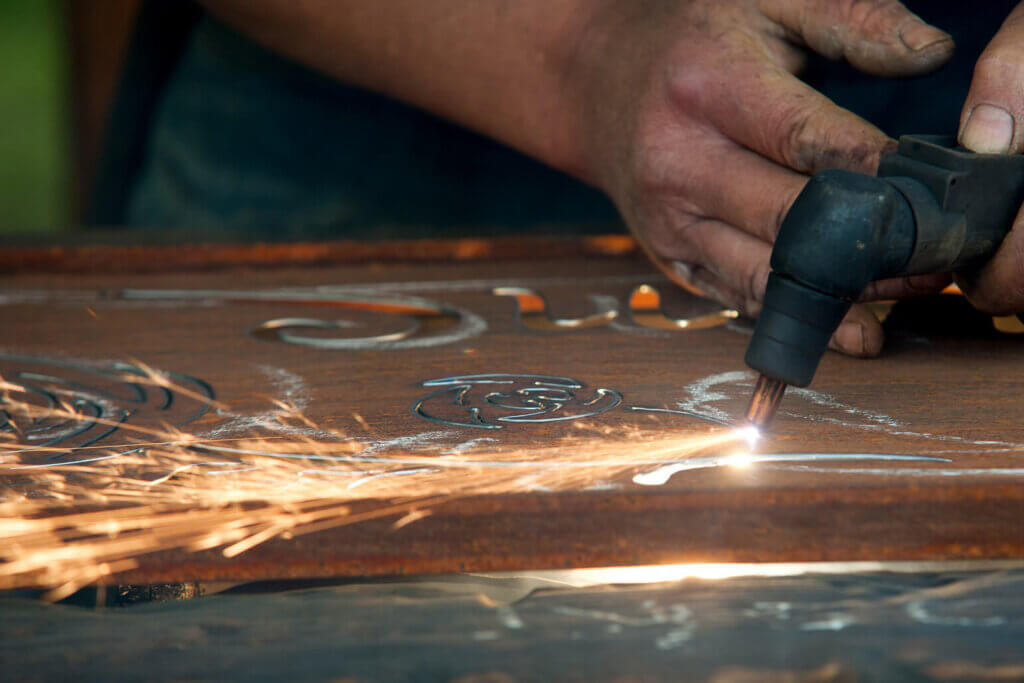
What features and functions are essential?
The plasma cutter uses high voltage to convert gas into plasma. Therefore, it needs a compressor to produce the compressed air. Especially with special offers, it may be that no compressor is included in the delivery. In this case, it is important to buy a suitable compressor as well. It is also worth taking a closer look at the cooling system. Cooling with fans is only safe if the plasma cutter does not exceed a certain amperage. If in doubt, and if the amperage exceeds 225 amps, it is better to buy a unit with water cooling. Various connections, hoses and nozzles belong to a plasma cutter. These must be included in the delivery. It is advisable to check that everything is present and free of defects before buying.
Important details
If you want to use your plasma cutter not only in your workshop at home but also in other places, you should choose a device that is not too bulky and heavy. Energy-efficient devices are not only easy on the wallet, but also on the environment. Beginners in particular should choose an appliance that is easy to operate and has clearly written instructions for use. Many companies also offer videos with instructions. Connections and hoses can become damaged even with careful use and must then be replaced. Does the company also offer these as accessories for purchase?
Useful features and extras for beginners
If you are a beginner or only need the machine occasionally to cut metal, you will be satisfied with a simple plasma cutter. It is easy to use and is an excellent way to learn the basics.
Useful features and extras for advanced users Cutting quality and speed, as well as the precision of the cuts, become increasingly important as the work moves away from simple cutting tasks. The versatility of the tool also becomes more important as the work becomes more complex. For example, advanced users usually want greater intervention in the processes, for example by being able to regulate the cutting current or the speed of the cut. Units with a higher amperage can cut thicker and more conductive metals than units with a lower amperage.
Essential accessories for safety
If you want to avoid damage to yourself, the plasma cutter and the working environment, there are some accessories you should not do without. This definitely includes the appropriate protective clothing consisting of a welding jacket, welding helmet and goggles, welding gloves and a respirator mask. The surface on which the plasma cutter stands should be fireproof (welding table). You also need a spark protection mat to protect against flying sparks. As a general rule, work with a plasma cutter should only be carried out in well-ventilated rooms without hazardous materials.
Important tips on handling and care
With normal use, a plasma cutter, unlike other cutting devices, shows little signs of wear. However, if possible, the individual components should not come into contact with dirt or oil. Spare parts such as hoses or access nozzles can be easily replaced by the user. However, only spare parts that fit the plasma cutter in question should be used – if possible, the original spare parts from the manufacturer. Otherwise there is a risk of accidents or damage to the unit, for example due to overheating.
Also, users must never carry out repairs themselves, as this can also result in serious malfunctions. It is better to have repairs carried out by the appliance manufacturer. During the warranty period, the warranty expires if the plasma cutter is opened.
After use, many units need an after-cooling period so that the cooling system (fan or water cooling) can cool down the heated electronics. Therefore, such devices must remain switched on for some time after the cutting work has been completed.
Things to avoid when using a plasma cutter
Although it is sometimes tempting or seems obvious, it is important never to use a plasma cutter other than for the purpose for which it is intended. The instructions provided clarify what materials the plasma cutter is approved for, how it should be handled and what it is not suitable for. For example, thawing pipes with the plasma cutter is not permitted.
Important questions and answers at a glance
1. For whom are plasma cutters suitable?
Thanks to the fair prices, plasma cutters are now also worthwhile for hobby craftsmen who only sometimes want to cut metal, as an enrichment for the home workshop. For all those who work with metal more often, a somewhat more sophisticated device with a wider range of functions is also worthwhile.
2. Is it worth buying an inexpensive machine?
Absolutely, because there are now also high-quality tools available at comparatively low prices.
3. Are there also mobile devices?
Yes, these are especially worthwhile for those who want to use their plasma cutter outside their workshop.
4. Which metals can be cut with plasma cutters?
All conductive metals such as aluminium, steel, stainless steel, brass, copper and iron.
Conclusion: Plasma cutters have long since become attractive to home users and hobby craftsmen. Reasonable prices and solid performance can already be found in entry-level devices, and those who want to upgrade can access a wide range of devices and accessories.