Pillar drill purchasing advice: how to choose the right product
- What You Need to Know
- The bench drill is worthwhile for home users and craftsmen who want to tackle demanding drilling jobs.
- Before buying, the consumer should note that the bench drill is not suitable for drilling walls.
- When choosing a bench drill, it depends on the desired purpose.
- The term bench drill refers to the small drilling table that is attached to the column of the machine, rather than the fact that the machine stands on a table.
What is a pillar drill and what makes it special?
Ambitious hobby home craftsmen and professional craftsmen in the wood and metal sector can hardly do without a drill. However, an ordinary hand drill is usually not enough to perform the many different drilling tasks. Often a bench drill is used, which is more powerful, drills more precisely and provides a better hold for the drill piece.
The bench drill is a stationary machine with electric drive. The most important task of a bench drill: it drills holes of various sizes in drill pieces made of wood, metal, plastic, glass and stone. However, this task is also performed by other types of drilling machines such as the ordinary cordless drill, the impact drill or the pillar drill. So in what way does the bench drill stand out from the other variants?
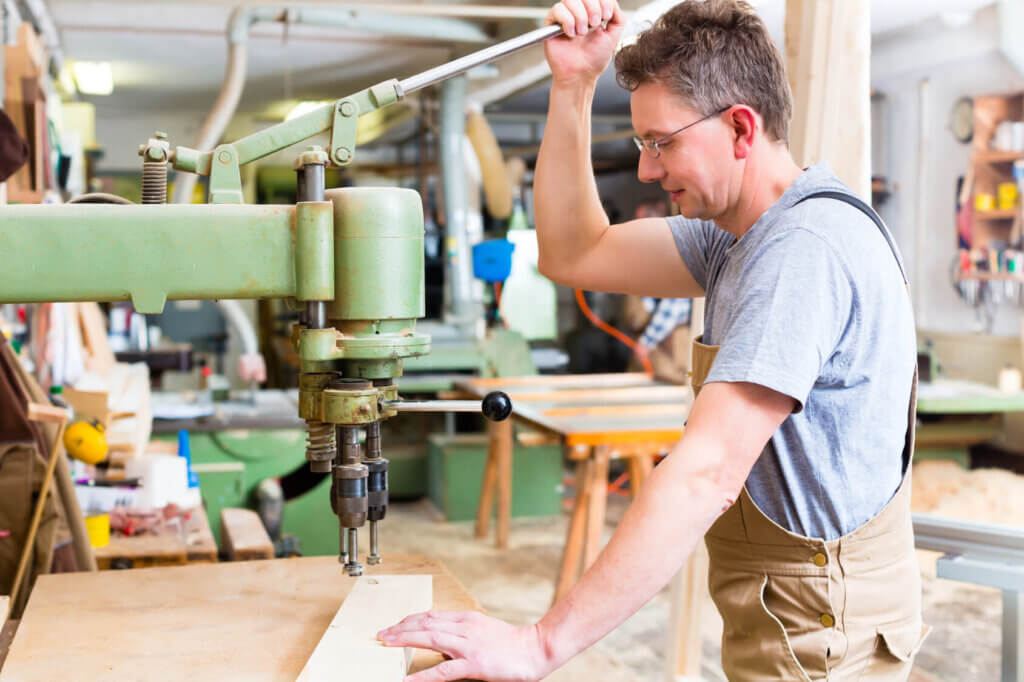
Pillar drill versus cordless drill
If you compare the manually held cordless drill with the stable bench drill, you will immediately notice that the drill of the bench drill can only be moved in one direction: vertically downwards. The cordless drill, on the other hand, can be used at any conceivable angle because the machine operator holds it loosely in his hand. This means that it can drill vertically through firmly clamped workpieces just as well as it can drill horizontal holes for a shelf in a wall.
Does this mean that the bench drill would be at a disadvantage compared to the cordless drill? No, because in fact there are a number of reasons why the bench drill beats the battery-powered hand drill in its variety of uses. The drill and the chuck that holds it are sturdily attached to the bench drill, which in turn is secured either by its weight or fastening mechanisms to the work table or workbench. Although this leaves little room for manoeuvre in terms of drilling direction, the device offers particularly high stability when drilling in one direction.
The fact that the drill drills reliably and safely vertically means that it can also be used to drill complicated holes. Some models have a tilting drill table. With it, inclined drillings are also possible.
The special challenges
One of the difficult drillings is the drilling of a rounded workpiece, for example a sewage pipe. If you work on such a pipe once with the cordless drill and then with the bench drill, you will find that the latter machine is superior for this task. With the cordless drill, craftsmen can easily slip on the surface because of the lack of stability. This ruins the workpiece and can lead to injuries to the machine operator. It does not matter whether the pipe is fixed in a vice when drilling, for example, because the weak point is the cordless drill that is not fixed. With a bench drill, on the other hand, such slippage is not possible. If you fix the workpiece securely, you can drill clean holes even in rounded surfaces.
If the machine is to make a series of identical holes on a workpiece, a bench drill is the best choice because of its high precision. This is because the drill cannot change drilling direction and angle. Even if the machine operator is not concentrated or distracted, he can drill very precisely – more precisely than is possible with a cordless drill. He only has to place the drill in the correct position and lower it. Uniform drilling is thus very easy.
Pro Points
- safe drilling even with difficult drilling tasks
- Uniform drilling in series possible
- Perfect right angle when drilling straight drill pieces
- simple operation
- Many practical extras available
Drawbacks
- Can only be used stationary
- No percussion function
- No battery operation
- Usually expensive
Selection and purchase criteria
When buying a bench drill, buyers have a choice between many suppliers: Bosch, Einhell, Proxxon, Optimum, Elamag, Flott, Silverline and Scheppach are well-known and less well-known among them. The most important buying criteria include
- the motor power,
- the drilling depth,
- the drilling stroke,
- the chuck clamping and
- the speed range.
Some models also have extras such as LED lighting or a laser. Table drills do not have a percussion function. If you need one, you should buy a hammer drill.
The name of the bench drill
Why is a bench drill called a bench drill? Actually, the name has nothing to do with the fact that the drill is placed on a table to work at an appropriate working height. This is also possible with a pillar drill. Although the machine is often used on tables, the name refers to the fact that the drill has its own small table on which the piece to be drilled lies during drilling. It can also be securely clamped there so that it does not slip away during drilling.
But not every bench drill comes with clamping mechanisms. The machine operator may have to improvise. If a stationary drilling machine that stands on a table does not have its own table in which the device is integrated, it is strictly speaking not a bench drill.
Different types of bench drills
Bench drills can differ greatly from each other. However, they have one basic design in common, which is the same for all models. The drill base provides the necessary stability. This is achieved by its weight or by fastening it to a base with the help of bolts and nuts.
In the upper part of the machine there is a housing in which the motor is hidden. It is equipped with various switches with which the machine can be operated. In addition, the drill chuck, which holds the drill, is located at the front under the housing. It usually has three chuck jaws, which are also called three-jaw chucks. In addition to the obligatory table, the machine has a lever or wheel that can be used to lower and raise the drill bit when drilling into the workpiece. Apart from this, bench drills can have numerous differences, which we explain in more detail below.
Powerful machines for complicated tasks
Bench drills are known for having a particularly high power. This lies between 200 and 1,000 watts. How many watts are useful for which tasks? It is said that amateur do-it-yourselfers get along well with machines that have 400 to 600 watts. But it always depends on what the machine is supposed to do. In the field of model making, bench drills with a power of 200 watts are sufficient. For drilling through hard materials such as metal, 600-watt machines are a good choice. For a wide range of tasks, which can sometimes be complicated, the buyer should go for one of the most powerful machines.
The idle speed determines the drilling speed
The idle speed indicates in revolutions per minute how fast the drill chuck rotates, i.e. how fast the machine operator can drill holes. There are two indications: the minimum and the maximum idle speed. The speed can be adjusted. There are two ways in which this can be done: On some models, the speed can be adjusted in three to twelve steps, while on others it is infinitely variable.
Many craftsmen prefer the stepless variant because they can better adjust the drilling speed to different materials. But which speed is optimal? That depends on the materials to be worked. Hard materials such as steel can be worked better in the low speed range, while soft materials such as wood can be drilled well in the high speed range.
Belt versus direct drive comparison
The buyer can choose between a bench drill with a belt drive and one with a direct drive. Both variants have advantages and disadvantages.
This is what the belt drive offers:
Pro Points
- cheap
- smooth running
- the better choice for home use
Drawbacks
- belt is susceptible to wear
The direct drive has the following advantages and disadvantages:
Pro Points
- smaller
- comfortable, as speed control is electronically
- Maintenance-free for a long time
- faster speed change
Drawbacks
- more expensive
- louder
- Torque does not increase automatically at low speeds
The weight provides stability
The weight of the machines can be as little as ten kilograms or as much as over 20 kilograms. A high weight makes it difficult to carry the bench drill. However, since it is a stationary machine, it usually stays in place. Usually, a heavy weight ensures a secure stand and prevents the machine from slipping during use. To avoid an accident (for example, someone or something bumping into the machine), it is advisable to securely fasten the machine to the ground. Many machines can be mounted on a table.
A real bench drill includes a drill table
The drilling table is height-adjustable on most models. This makes it easier to drill very large and very small workpieces. Depending on the model, the table can also be swivelled and tilted. This makes it possible to drill at an angle of up to 45 degrees. Furthermore, the tables vary in size depending on the model. As a rule, the length and width vary between 20 and 30 centimetres.
The drilling stroke refers to the maximum depth of the drill bit when it penetrates the drill piece. The drilling stroke is the distance the bench drill can be raised and lowered. Lifting and lowering is done by the machine operator himself. For this purpose, there is a lever or a wheel on the machine. The drilling stroke is between 50 and 160 millimetres. Bench drills with a drilling stroke of 90 or more millimetres are more suitable for special drilling. The drilling stroke is also called the drilling depth.
The drill chuck holds the drill
Modern drill chucks with quick-action drill chuck locks allow the drill bits to be changed quickly without the use of tools. The minimum and maximum width of the drill bits on a machine is indicated by the drill chuck span. For most bench drills, these values are between 1.5 and 16 millimetres. Professional craftsmen should choose a machine that covers as wide a range as possible. For hobby home craftsmen, it depends more on the purpose. In model making, machines with the lowest possible drill chuck spans are the better choice.
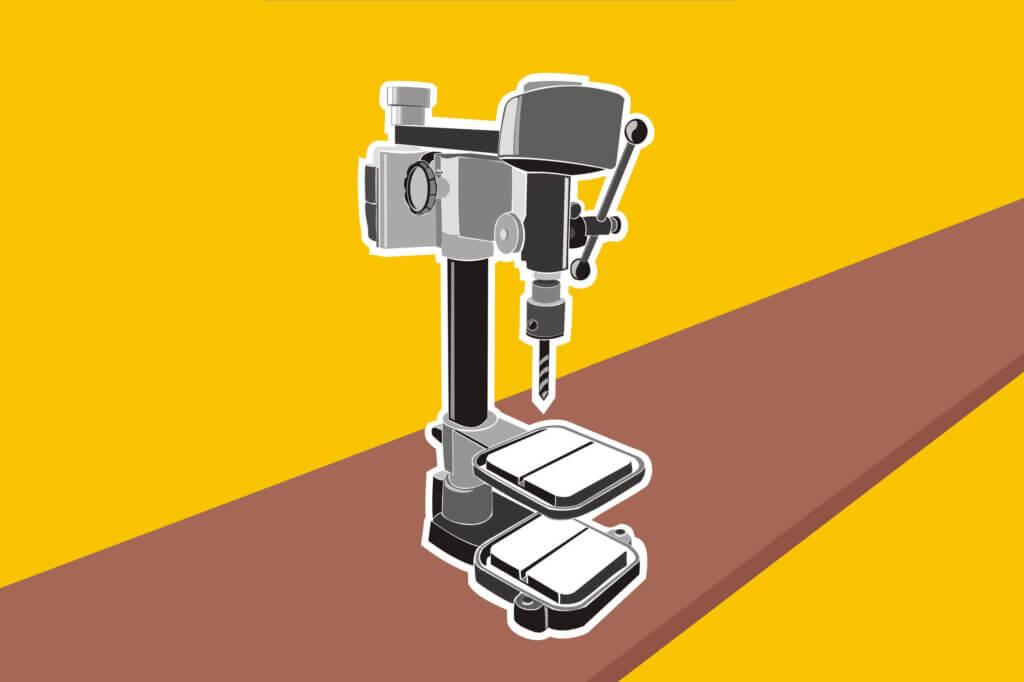
The machine operator should observe safety precautions
There are a number of safety precautions that the machine operator should observe during operation. These include wearing tight clothing and safety glasses, not wearing gloves of any kind and tying up long hair. There are also machines that offer special safety features, but these are not mandatory. Typically, for example, there are extra protective components that protect either the eyes or the hands from flying chips. An emergency stop switch also proves valuable in an emergency. If a dangerous situation arises, the machine operator can use it to put the bench drill into stop mode at the push of a button. Another safety feature that some machines come with from the factory is short-circuit protection.
LED lighting illuminates the work area
In workshops, lighting is not always perfect. An integrated LED lamp can do a good job when using the bench drill.
The laser shows where the drill bit is drilling into the workpiece
The laser on a bench drill shows where in the workpiece the drill is drilling if the machine operator does not make any other adjustments. This makes it possible to drill highly precise pinpoint holes. Drilling is thus easier and more comfortable.
The digital display as a little luxury
A digital display shows important information at a glance, including the set speed or the current drilling depth.
The depth stop for more precision
A depth stop helps to achieve the desired drilling depth exactly. It is usually a simple metal rod that lies parallel to the drill and can be adjusted. It can be locked in place with a clamp. After all, the drill can only penetrate a workpiece as deep as the rod allows.
Not all power connections are the same
Bench drills are available with two types of power supply: a 230-volt or a 400-volt connection. The larger the holes drilled and the harder the material to be drilled, the more likely the buyer is to buy machines with a 400-volt connection.
Our buying guide
What consumers should know if they want to buy the product
Bench drills do not tolerate high humidity, which can severely damage the machine. So before buying, consumers should find a room where conditions are favourable in this respect.
It also makes sense for the buyer to provide a base on which to fasten the bench drill with nuts and bolts. This will prevent the machine from accidentally tipping over or slipping.
What consumers should look for when choosing
Bench drills are available for purchase in online shops and in local shops. Those who prefer to buy locally can benefit directly from good advice, which is not included in online purchases. In addition, the prospective buyer can try out on site whether the handling, size and design suit him or her.
Which functions and features are a must
With regard to safety, the user has to consider a few things. Flying sawdust, for example, from drilling metal, can damage sensitive eyes or cause wounds on the hands. An emergency stop switch is a very important safety feature because it can save lives in an emergency.
We also recommend a drill chuck with a drill chuck quick release. There is no faster and more convenient way to change drill bits!
Which functions and features are useful
If you don’t drill often, but value precise drilling, you should get a bench drill with a laser. The laser helps to drill precise holes.
If necessary, when buying a bench drill, the consumer should choose a model that has a swivelling and tilting work table.
Which functions and features are superfluous
A digital display is a nice gimmick, but nothing more. Values such as the drilling depth or the current speed can be displayed easily and comprehensibly without it.
Equipment recommendations for beginners
- Bench drill with belt drive
- swivelling, tilting and height-adjustable drilling table
- drill chuck with drill chuck quick release
- laser and LED illumination
- Depth stop
- Safety equipment
Equipment recommendations for advanced users
- high power
- Idle speed in a wide speed range
- direct drive
- swivelling, tilting and height-adjustable drilling table
- 400 volt machine
Care and safety tips
Tips and hints for handling the product
A bench drill can be dangerous if operated incorrectly. Hair or clothing can get caught in the drill, the drill can break off and shoot away, and the drill chips also pose risks. If you have never worked with a (bench) drill before, you should first have a professional show you how. It is also important to know the safety instructions.
Tips for safe use
- tie long hair securely at the back or top of the head
- Do not wear gloves when using
- do not wear loose clothing, prefer tight-fitting clothing
- wear short sleeves or roll up long sleeves safely
- scarves, necklaces and arm jewellery must be removed before use
- Wear safety goggles
- Wear ear protection if necessary
On the machine
- check all important components before switching on
- fix the workpiece securely before drilling
- before the operator removes the workpiece from under the drill, the drill should come to a stop
- regularly remove chips from the drill
- Before replacing the drill, switch off the machine and unplug it
Tips for care and cleaning
Good care and regular cleaning will ensure a longer life for the bench drill.
The care
- while the machine is not in use, it should not be connected to the mains supply
- Rub the drill regularly with grease
- If necessary, also treat the quick-action chuck with grease
Cleaning
- After work, unplug the machine and clean it.
- Wipe the machine with a damp cloth only, do not allow water to get into the machine
- Do not leave switches, handles and moving parts slippery, for example, clean them of grease
- between several drilling operations, clean the work table, the drill and other parts of the machine of chips; never use your bare hands, but a brush or hand brush, a hoover or compressed air compressor are also helpful
- Follow the manufacturer’s other cleaning tips in the instructions for use
Questions and answers
How does a bench drill work?
After inserting the desired drill bit, the machine operator clamps a drill bit firmly in the machine so that it is securely fixed. Clamping by means of a clamp or vice is another option that has proved successful. He then switches on the bench drill. With the help of a lever, he can lower the drill vertically. With a depth stop, if present, he determines the maximum drilling depth before drilling. After the desired depth has been reached, the machine operator raises the drill again with the lever. He can then switch off the machine and, if necessary, reposition the workpiece for another drill hole.
How is a bench drill constructed?
The entire machine stands on a stable base. From this, a column rises vertically into the air. At the highest point, the motor and other components, for example a gearbox, are mounted and hidden behind a cover. At the front, below the motor, is the drill chuck in which a drill bit can be clamped. A lever or wheel with which the drill can be lowered is also attached to the upper part of the machine. Below the drill chuck, a small table is attached to the column, on which the workpiece rests during drilling.
What do you have to pay attention to with a bench drill?
During drilling, the machine operator should make sure that the workpiece is securely fixed. Otherwise, the energy of the machine can whirl it around or throw it away. In addition, there are also some safety rules that the user should urgently observe in order not to endanger himself or herself and not to damage the machine.