Impact drill purchasing advice: how to choose the right product
- The most important facts in brief
- In contrast to normal drills, percussion drills not only rotate the drill bit, but also hammer it forward with a jerk.
- Their higher penetrating power makes them suitable for harder materials.
- A second gear, a reversed rotary mechanism and an impact mechanism that can be switched off make working more comfortable and versatile.
- Depending on the material to be worked on, a different drill attachment is suitable.
The difference to ordinary drills
For hobby craftsmen and professionals alike, a drill is an essential part of their repertoire. If extensive work is to be done or if a surface made of very hard material has to be worked on, an impact drill is recommended. This differs from normal drills primarily in its technology and is therefore one step ahead of them. While conventional machines are suitable for working on wood, plastic and metal, they quickly reach their limits when working on stone and concrete. This is where impact drills play their trump card: They not only rotate the drill head, but also generate a forward movement at the same time, thereby hammering the drill bit into the material to be worked on.
How the percussion mechanism works
The impact is generated by a motor shaft inside the impact drill. This moves two discs with slanted teeth, one on top of the other, back and forth. This mechanism is called the ratchet impact mechanism. It can optionally be switched off so that the device works like a normal drill. It then does this with a lower speed of the drill head, which also makes it easier for the user to guide.
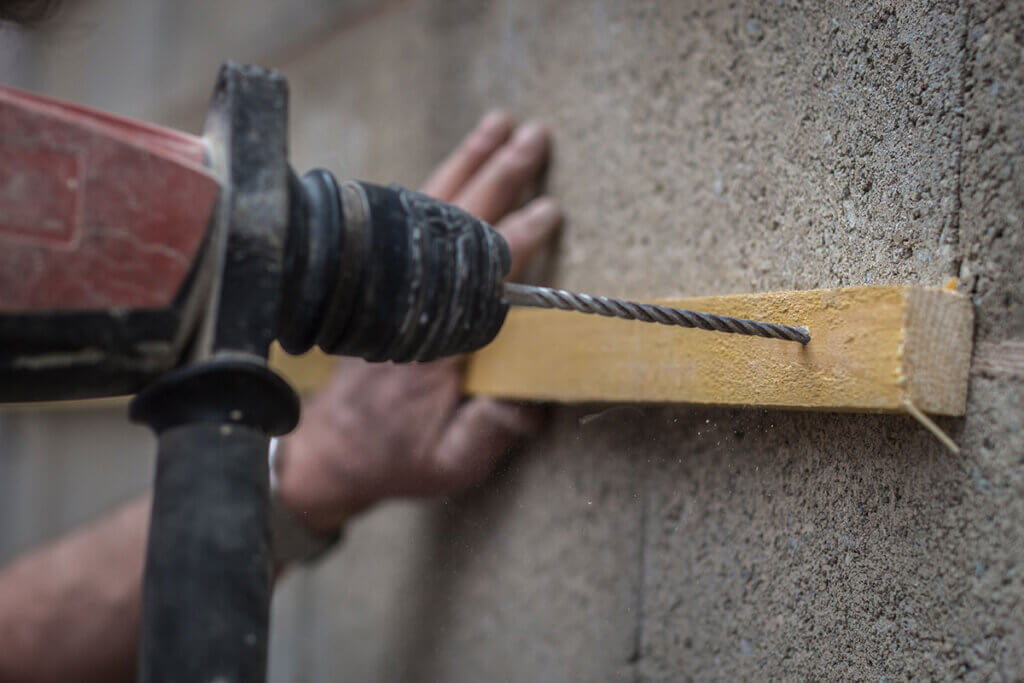
The drill, whether it has an impact mechanism or not, gets its power from a power source. Some models are equipped with a cable or mains adapter for this purpose, but there are also cordless drills. The latter have the advantage that they are more compact and can therefore even be used with one hand. However, they usually have no less penetrating power and a lower speed, which is why they are not suitable for all materials. In addition, the runtime of a rechargeable battery is limited. If you are working for a longer period of time or need to work on masonry made of solid concrete, you should go for a heavier device.
Components of an impact drill
Because of the strong vibrations and sometimes heavy weight, the user must have a firm grip on an impact drill. If you are careless or operate it incorrectly, it can slip out of your hand or cause annoying damage. To prevent this, many machines have two handles one behind the other, usually with a non-slip soft-grip surface. This also makes it possible to apply more pressure to the surface to be drilled through.
Most drills also have a switch that reverses the direction of rotation of the drill. This function is particularly useful if the drill has become stuck in the wall. If it rotates briefly in the other direction, it is free again and you can continue working. Another option is to switch to second gear, which is available in high-wattage impact drills. This drills faster, but with less power. This is advantageous for drilling smaller holes.
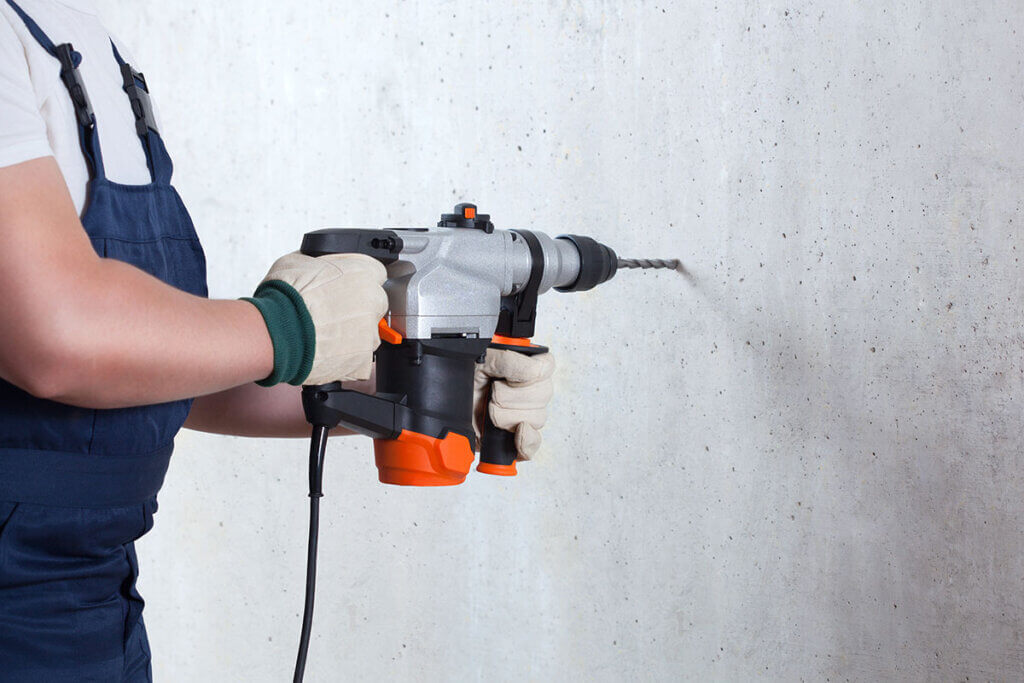
Some machines have a so-called quick-action chuck for fast changing of the drill heads. This allows the drill bit to be unscrewed with one hand and replaced with another. Small machines up to about 500 watts often do not have such a device and you have to resort to the slightly more cumbersome method of changing with a chuck key. This is called a toothed rim drill chuck, which encloses the drill very tightly. This means that even larger drill bits can be held well, whereas the diameter of the quick-action chuck is limited.
Drill attachments
Depending on the materials you want to work with, different drill attachments are recommended. At first glance they look similar, but the differences are in the attachment tips, which are suitable for different materials.
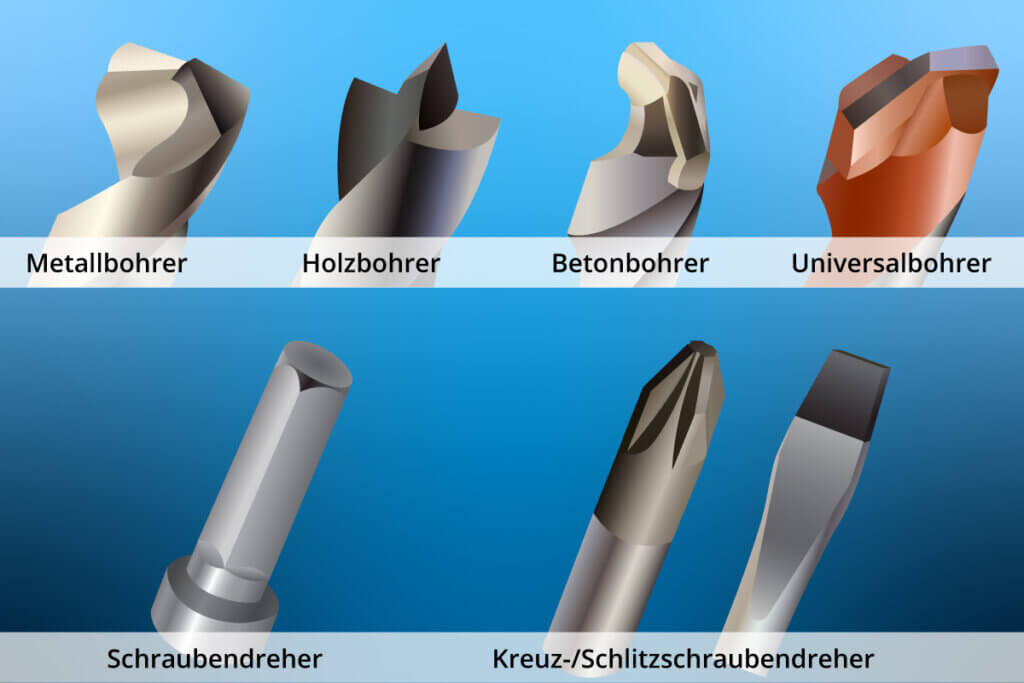
Masonry drill
The cutting edges of this drill can be blunt or ground, the tip is wedge-shaped and resembles a slotted screwdriver. Ground versions are used for tiles or porous bricks; blunt ones are specially designed for impact drills. These are used to hammer into stone or concrete, materials that are difficult to drill through.
Wood drill
The wood drill has a small centred point and two sharp, deeper cutting edges. It can be used to work on all kinds of wood or even chipboard. The cutting edges are longer on the outer edge. This makes it easier to cut through the wood fibres and produces a clean hole.
Metal drill
The tip is conical and much flatter than that of the wood drill. The drill is made of a special high-speed steel and often has a coating, such as titanium. In addition to various metals such as iron, copper or brass, it can also be used to work on plastics.
Universal drill
This drill is suitable for surfaces made of different materials. Just like a masonry drill, it also has a ground tip made of hard metal, which can even be used to work on wood. However, it is not a long-term substitute for a drill bit designed specifically for a single material.
Screwdriver
In addition to drilling holes, you can also use a special attachment to turn screws into the wall. However, this is only possible if the speed of the machine can be limited. Otherwise, the drill head would rotate too fast to get a screw into the wall. Due to the high rotation, you would quickly slip or destroy the screw head.
Power of percussion drills
Impact drills are available in different sizes with different power. Smaller models are intended, among other things, for hobby craftsmen who only do a few elaborate jobs. With a power of up to 500 watts, they are suitable for wood and thin surfaces, for example. However, you cannot always rely on functions such as a quick-action chuck or speed regulator here.
Larger models up to about 750 watts, on the other hand, are often better equipped, for example with a second gear. As all-round models, they are very well suited for many professional and everyday tasks.
The largest versions of impact drills have an output of at least 1,000 watts. With a length of up to half a metre, they are indeed large and heavy. On the other hand, it is even possible to drill holes in reinforced concrete with these machines. In general, you can say: The higher the wattage and thus the power, the harder materials can be worked well with the drill.
When the impact drill reaches its limits
Even with a high impact rate and an appropriate drill attachment, drilling in concrete is a laborious affair – for man as well as machine. If you want to work on it for a long time, the device may eventually run hot. For extreme work on hard walls, you might want to switch to a hammer drill. This is driven by a percussion mechanism with compressed air and can penetrate hard material with just a few strong blows.
Cleaning for longer life
To keep your impact drill in good condition and to ensure consistently good performance, you need to take proper care of the tool. After each day’s work, you should at least dust it with a cloth. Grooves and ventilation slots can be cleaned with a small brush. Otherwise, they will gradually become clogged with dust, which may cause the motor to overheat.
When you take the drill out of the holder, knock the dust out of the chuck every now and then, otherwise the mechanics inside can get stuck. From time to time, you should also put a few drops of motor oil in here to ensure smooth running. For storage, the drill is kept in its case, which is not included with every device. This protects it from dust if it is not used for a longer period of time.
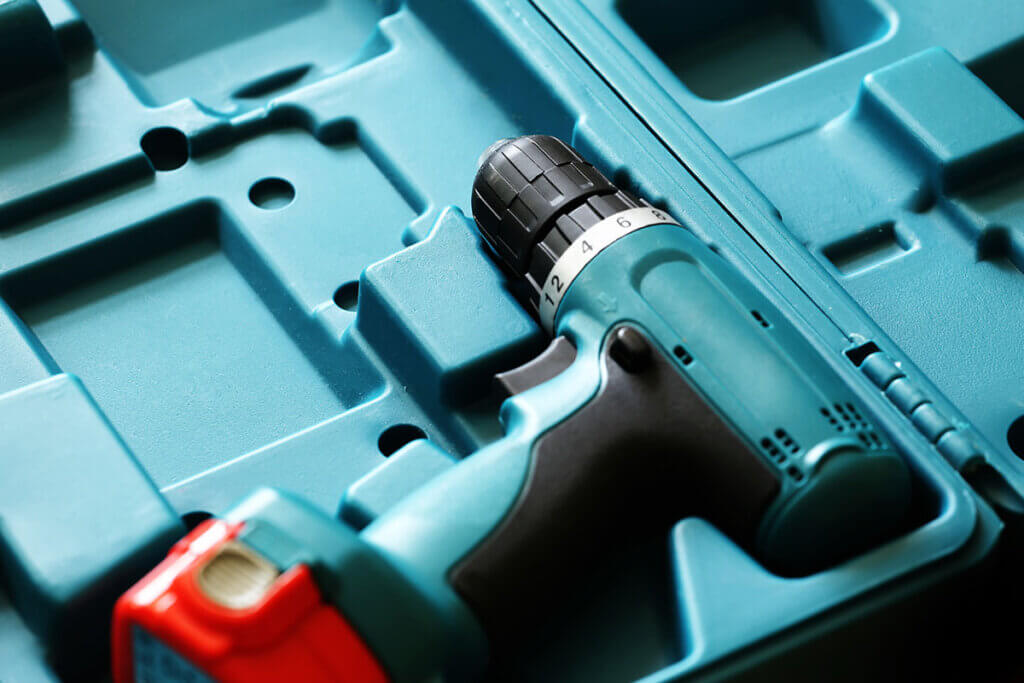
Protective measures
Especially if you are going to work with the drill for a long time, you should wear hearing protection. Most machines work at a volume of about 100 decibels, which is equivalent to the volume of a rock concert. Safety goggles and respiratory protection are also advisable, as dust is produced especially when drilling into concrete or wood. If you work with the machine for a longer period of time, your concentration may decrease at some point. In addition, it is tiring in the long run to hold the heavy tool properly. Therefore, plan rest breaks if necessary.
Drilling tips
Where there’s planing, there’s chipping – and where there’s drilling, there’s dust. Whether it’s wood or masonry; at the latest when you pull the drill attachment out of the hole, dust or fine wood chips trickle to the floor. Ideally, you should ask someone to hold a hoover directly under the hole at the same time as you are drilling, so that the dust is picked up directly.

However, if no helper is at hand, you can resort to a little trick and stick an envelope under the hole where the dirt is collected. For holes on the ceiling, you can make a hole in a yoghurt pot or similar container and attach it directly to the drill attachment. This way the dust does not trickle down onto you.
Drilling on smooth tiles is not so easy because you can easily slip when attaching the drill. You can get a better grip on the drill head by sticking a cross with masking tape on the spot where you want to drill. And if you are not sure whether the drill has gone deep enough, mark the correct depth on the drill with a piece of insulating tape.